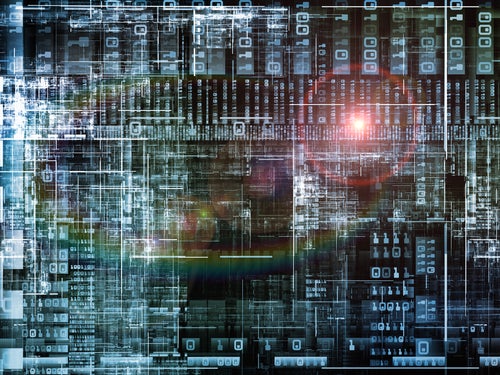
Concept: German company TK Elevator has rolled out a cloud-based, real-time monitoring and predictive maintenance platform called MAX. It collects data on components, systems, and performance to assist building owners and managers in increasing elevator and escalator uptime. MAX also assists facility staff in monitoring and controlling their equipment, as well as improving passenger safety using digital emergency services.
Nature of Disruption: Max uses cloud technology, big data, and ML to provide property owners and managers with operational and maintenance insights. Through real-time diagnostics, this IoT system improves overall elevator availability by eliminating out-of-service situations. MAX can predict maintenance issues and send alerts to elevator engineers to replace components and systems before the end of the product lifecycle. It collects data from MAX-connected elevators all over the world, including door movements, trips, power-ups, car calls, and problem codes. This information is transferred to the cloud, where special algorithms look for trends and calculate the equipment’s operation and remaining lifetime. It can provide the technician with exact and predictive diagnoses in real-time, showing where intervention is required.
Outlook: With MAX’s data-driven maintenance technology, TK Elevator intends to transform the elevator business by cutting downtime by up to 50%. It provides real-time alerts to service engineers and technicians on pre-issue repairs, making property owners more proactive with customers. This involves arranging repair tasks ahead of elevator breakdowns and during periods when the building is least crowded. It can also assist building managers and users in avoiding the frustration and inconvenience associated with out-of-service elevators. MAX also comes with MAX Link, a digital emergency communications system that eliminates the need for costly analog phone lines.
This article was originally published in Verdict.co.uk