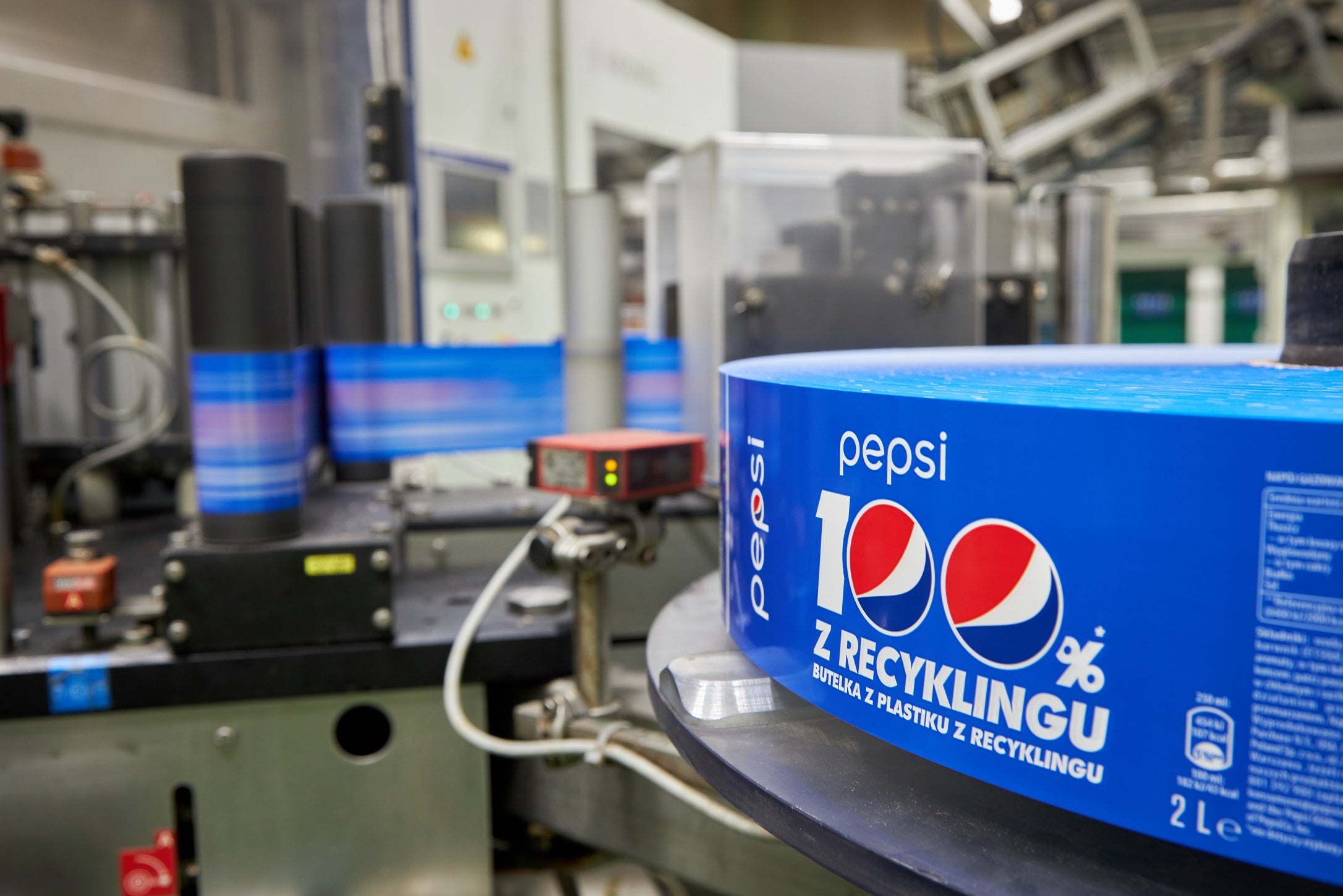
Drinks producers, already significant users of automation in their manufacturing, are speeding up their investment in the technology.
Factory floors are filled with machines that churn out precise recipes time after time, creating products automatically dispensed into the receptacle of choice, before being shunted around on snaking conveyor belts until they reach packing and palletisation.
Over time, these machines have got quicker, more accurate and much more efficient and the need for human intervention has reduced. However, when you visit the factory floor of any major beverage company, you are still likely to see human staff busy performing a range of tasks and functions.
Nevertheless, according to drinks companies and suppliers of automation technology, some of the roles once performed by humans are slowly disappearing as a new generation of tech – some of it enabled by artificial intelligence (AI) – is rolled out.
Hitting ESG targets
There have typically been a number of reasons why drinks companies use automation. For starters, it contributes to improve quality control, enables companies to make efficiency gains and also helps to keep workers safe in what are often potentially hazardous factory environments.
Drinks companies are also investing in the technology for new reasons. For instance, major Coca-Cola bottler Coca-Cola Europacific Partners (CCEP) is investing in automation across its manufacturing plants as it believes the technology can play a role in the company hitting its target of reducing carbon emissions across its value chain by 30% by 2030 and meeting its overall ambition of reaching net zero by 2040.
At its site in Sidcup, in south-east London, the company runs ten production lines that use a mix of mechanical arms and palletisers, with the site able to produce 10,000 bottles, cans or pouches every minute – the site is scheduled to package a mind-boggling 130m unit cases in 2023 alone.
There are roughly 20,000 pallets on-site that are managed through the use of ‘pick-and-place’ cranes as part of an automated storage and retrieval system (ASRS).
“This system moves pallets to and from their storage in the warehouse, placing them at the feet of the conveyor,” explains Rory Kerr, operations director at CCEP’s Sidcup site. “Mechanical arms load containers into each pack and a robotic palletiser then constructs each pallet, putting together packs of four, eight, 12, 18, 24 and 30 cans. For each of the can pack sizes, a different programme configuration is used, all of which has been coded on-site.”
Kerr says the introduction of the ASRS has seen efficiency increase across CCEP’s supply chain and it has also enabled the company to save 3,687 tonnes of CO2 per year.
In recent months, the factory has also seen the development of a high-speed canning line, which Kerr says is “capable of producing 2,000 cans per minute and is an integral part of elevating the site’s production capabilities, while also accelerating carbon savings”.
Managing the process
Rival beverage business PepsiCo has also invested in drinks automation across its business. Paul Campbell, supply chain senior vice president for the company’s operations in Europe, says in beverage manufacturing its main focus is on automating filling lines and packaging equipment, as well as automating some of the tasks that help to improve the efficiencies of its operations.
“This includes packaging equipment, such as fillers, labellers, packers, palletising equipment and stretch wrappers,” says Campbell. “We automate tasks such as change-over management, mould changes on blow moulding equipment and machine set-ups during format changes.
“We have also fully automated processing, blending and mixing operations. We use performance supervision systems that control the automatic valves, pumps and all the auxiliary equipment. Over the years, the change from manual swing bend panels to automatic valve clusters has completely changed the way we run our processing systems.”
And that is not the end of PepsiCo’s drinks automation push. It has installed fully automatic supervision and consumption systems for utilities meaning manual checks are no longer required, and it has implemented shop floor information management systems to capture live data and improve line efficiencies.
The company is also investing in automating warehousing systems, implementing automated guided vehicles (AGV) and introducing online, automatic equipment to check processes such as fill level and cap application to improve quality. “This allows us to conduct a real-time check on every individual package rather than sampling on a timed basis,” Campbell explains.
Another area of investment that came to the fore during the Covid-19 pandemic was the development of remote connectivity technologies and remote ‘original equipment manufacturer’ support capabilities, which Campbell says has been important for PepsiCo as it wrestles with challenges in securing skilled staff.
“This technology was utilised during the pandemic for the start-up of new lines and troubleshooting,” he explains. “In the wake of the pandemic, we also began to observe challenges regarding the availability of technical resources in several markets, and it is becoming harder to hire technically skilled people. As a result, further automation of tasks will be necessary to continue to improve our operations in these markets.”
Drinks automation could help labour pains
It is a view shared by Coesia, an Italy-based group that specialises in the provision of advanced automatic machines, packaging materials and industrial process systems.
A spokesperson for the company says some drinks manufacturers – and particularly those based in the UK – are exploring the idea of introducing greater levels of automation due to a lack of available labour.
“In the past it was the cost of labour and now it is the lack of reliable labour,” explains the spokesperson. “Companies are struggling to find people to work the lines every day. If companies can automate the simple repetitive tasks they can then use their reliable employees for more value-added jobs.
“Beverage companies will be putting their resources into whatever they can do to alleviate their labour problems in the shortest amount of time.”
The motivation for installing drinks automation technology may differ on a case-by-case basis but it appears the future direction of travel for beverage companies large and small is to continue to invest in this area thanks to the potential benefits on offer.
“As our operations become increasingly digitalised, we are aiming to implement the highest level of automation and latest technologies when investing in a new manufacturing line, while taking the financials into consideration,” says PepsiCo’s Campbell.
He adds the company sees “automation as an increasingly important commercial focus for the business”.
With the ongoing labour issues and environmental considerations at the forefront of the minds of the boards at many drinks companies, and with a new generation of technology such as AGVs, robotics and machines underpinned by AI slowly starting to become more commonplace on factory floors, automation looks set to play an even greater role in beverage production.