Like the vast majority of consumer goods companies, the bulk of the greenhouse gas emissions generated by spirits groups are Scope 3 – that is, indirect emissions that occur in the value chain.
These are distinct from Scope 2 (indirect emissions from the generation of energy bought and consumed by a reporting company) and Scope 1 (direct emissions from owned or controlled sources).
As spirits companies work to reduce their Scope 1 and Scope 2 emissions, one early-stage area of testing is the trialling of hydrogen fuel in distillation and in the production of glass bottles.
When ignited, hydrogen produces just heat and water as a result, making the gas a potentially enticing, carbon-free, fuel source and one that can help reduce a company’s emissions from manufacturing.
Blue and green
There are two main sources of hydrogen gas, which are often dubbed ‘blue’ and ‘green’. Blue hydrogen is sourced from natural gas through a process using fossil fuels that produces carbon dioxide as a consequence. As a result, distillers’ efforts have been focused on the production of green hydrogen.
Green hydrogen is created through electrolysis, using an electrical current to split the building blocks of water – hydrogen and oxygen – and passing the hydrogen through a membrane to capture it.
If renewable energy is used as the electrical source to split hydrogen from the water, the captured hydrogen fuel is considered ‘green’.
One of the issues in producing green hydrogen is the electrolyser equipment used to split water can be not only costly but inefficient. With energy being fed into the process, for it to be economically viable, more energy needs to be coming out in hydrogen fuel than is put in.
UK-based research and product development company Supercritical Solutions says it is trialling a more efficient electrolyser.
“We're developing the next-generation technology out of the UK that operates at a 95% efficiency level to produce high-pressure hydrogen. That means that we have a significant benefit relative to other technologies,” Supercritical Solutions co-founder Luke Tan tells Just Drinks.
“The challenge with the technology like ours and other novel technologies coming forward is that we aren't at the point where we have fully scaled up like the other ones are today. We aim to be at scale by 2030, producing hundreds of megawatts into gigawatts into 2030.”
Distilling trial
Suntory Global Spirits has been working with Supercritical Solutions to trial the use of hydrogen fuel at the whisky giant’s Yamazaki distillery in Japan. Hydrogen was used to directly heat a still during the distillation process. According to the Beam whiskey maker, the direct-firing technique can heat the still at higher temperatures than if using indirect heating by steam coils.
For safety reasons, conventional natural gas was used to start and end the burning during the trial. “We've delivered the trial using 100% hydrogen with great success,” Alistair Leckenby, environmental and sustainability manager at Suntory Global Spirits, says.
“There were no operational challenges, we were within the key parameters the team over in Japan look for in terms of temperatures that are achieved. We were able to replicate the process and production conditions that you get from using natural gas by using hydrogen.”
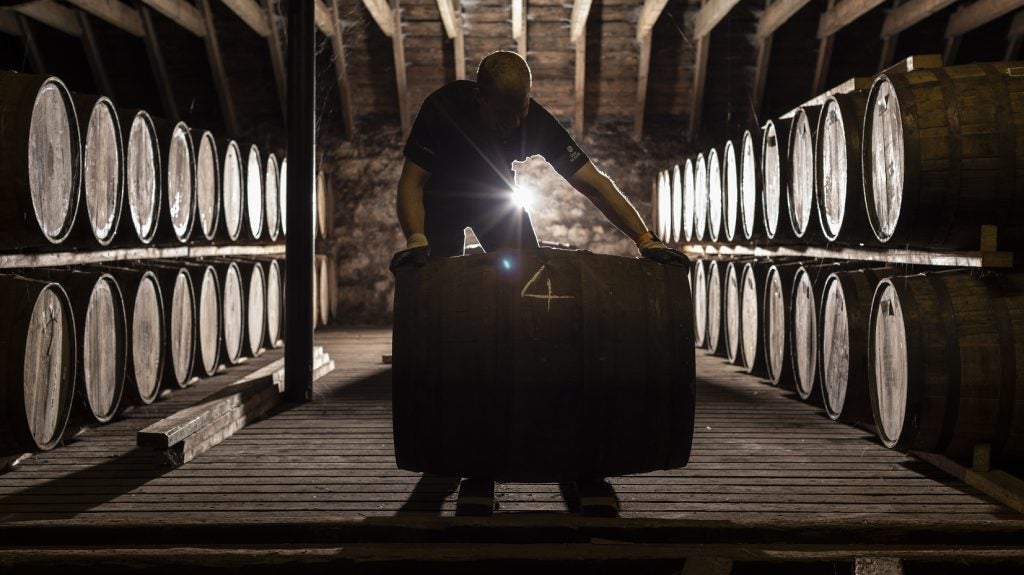
Suntory Global Spirits is aiming to use the process at its Glen Garioch's distillery in Scotland. However, that trial may be some time off as they have barrelled the whisky distilled in the Japan test and are awaiting its four-year maturation to ensure it is of comparable quality to spirit made through gas-fired distillation.
Firing glass
At Pernod Ricard, vodka-distilling subsidiary The Absolut Company is also testing the use of hydrogen technology in a bid to tackle the carbon within its supply chain.
The French spirits giant has teamed up with glass supplier Ardagh Group to use a partially hydrogen-fired furnace to produce bottles for Absolut vodka. At Ardagh’s factory in Limmared in Sweden, the company plans to power the glass melting furnace with 20% hydrogen gas.
“Hydrogen will be generated on-site using an electrolyser powered by renewable electricity,” factory MD Bo Nilsson tells Just Drinks.
“It is otherwise difficult to buy, transport and store enough hydrogen to support the scale of production at our Limmared facility – 140 million bottles of Absolut per year. This is not just a trial; from May of this year Absolut will be supplied all of its iconic glass bottles from this partly hydrogen-fired furnace.”
A large-scale glass furnace needs to be continually operating at 1,500 degrees Celsius. They can take days to reach this temperature and a sharp shutdown of the furnace could cause damage to the furnace itself.
“You need a substantial and stable supply of energy to maintain this ongoing high temperature and, to date, the industry has used natural gas to provide this stability,” Nilsson says.
“Ultimately, we believe that electrification, using renewable electricity, is key to decarbonisation. A hybrid furnace is currently under evaluation at our Obernkirchen facility in Germany, that will inform and support this transition for continuous production.”
Billy King, Absolut’s director of operations, says the cost of investment means collaboration is vital to decarbonise glass production. “Whether you’re talking about the electrification of furnaces, or whether you’re talking about hydrogen, these all come with a huge price ticket,” he says. “This is where you need partnerships, like the one Absolut has with Ardagh in Limmared, to make those things happen.”
Encirc is another glass manufacturer looking to hydrogen fuel as a means of reducing its emissions and is building a hydrogen-powered furnace at its glass plant in Elton in north-west England.
The company, owned by glass manufacturing major Vidrala, claims the furnace will reduce carbon emissions by 90% through a mixture of green electricity and hydrogen. Encirc is a major glass manufacturer for Diageo, which collaborated with them on trials for mass-producing ‘net-zero’ glass bottles.
“In the future (from 2030 onwards), as our furnaces reach the end of their natural lives, we plan to begin replacing them with much more sustainable furnaces,” a spokesperson for Encirc says. “In our Cheshire plant, we plan to use a mixture of hydrogen and green electricity. This will help to reduce the carbon footprint of bottles by up to 90%.”
Encirc’s factory in Cheshire is close to the location of a planned new hydrogen production plant that’s part of HyNet, a UK government-backed hydrogen production, storage and carbon capture project, due to get up and running by 2028.
Challenges ahead
The main users of hydrogen gas are large energy and chemical producers. They have the scale and infrastructure to produce and use the fuel and, secondly, they are already familiar not just with the fuel but the production and storage of hazardous gases.
These could represent barriers the beverage industry encounters as they trial changing to hydrogen. If they opt for housing the electrolysis process on site – as Ardagh Glass are trialling – the storage and handling of hydrogen gas could prove a challenge. Hydrogen may be a greener energy but it’s still a colourless, odourless and tasteless gas that’s highly flammable.
A solution would be the creation of hydrogen hubs used to create and store the gas for distribution to surrounding businesses, providing a similar set-up to regional power stations.
Supercritical Solutions’ Tan says that kind of network is being looked at in north-east England and in Scotland.
“Optimally locating or tweaking locations will allow you to support distillery one, two and three, and hence reduce the cost of production because you can produce a bigger electrolyser facility, producing lower-cost green hydrogen,” he says.
Tan believes that to encourage the wider use of the technology in the drinks sector might require a carrot-and-stick approach.
“At what point are the beverage industry going to be actually punished or taxed for that carbon content and their products? I don't think government knows that. I don't think the companies know that,” Tan says.
“But if we do start to put a price on how much it will cost companies to not decarbonise their products, I think we’ll see a much faster adoption of greener technologies because we'll be able to compare the cost of the investment to the cost that will be incurred if you do not invest. Right now, the cost incurred if you don’t invest is really unclear, so, it’s really hard to make a business case for investing in green technology.”
Tan believes businesses like Supercritical Solutions are helping to educate industries that haven’t needed or worked with this type of green technology and he says adoption of these alternative fuels will help drive costs down.
The use of hydrogen fuel in the beverage industry is nascent but, as companies work to make their operations more environmentally sustainable, more tests and trials are likely. The speed at which the technology could then be rolled out more widely remains an open question.