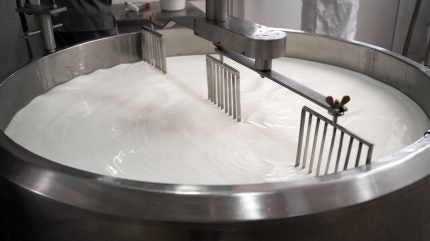
When it comes to providing both heating and cooling for industrial processing plants, such as dairies, heat pumps are significantly more energy efficient than traditional heating and cooling systems. Heat pumps use environmental heat sources like ground, air, or water, and available waste heat from the plant’s production processes to generate heating and cooling. Large-scale heat pumps are used to boost these lower-temperature heat sources to higher temperatures needed for industrial processes like pre-heating, pasteurisation, clean-in-place (CIP) and HVAC loads.
As they use energy available for free in the environment or excess waste heat and therefore avoid efficiency losses from combustion processes, the high efficiency of heat pumps can lead to lower operating and energy costs over the lifetime of the system, despite the initial system being more complex compared to traditional fossil fuelled boiler setups. Furthermore, when powered by green electricity, operating heat pumps can reduce carbon emissions up to 100%.
The European Environment Agency is focusing on waste heat recovery using high-temperature heat pumps to decarbonise European industries, including food processing[i], thus contributing to the EU’s net zero emissions target for 2050[ii]. According to the European Heat Pump Association (EHPA)[iii], over 60% of energy consumption in industry goes on heating, so increasing the use of renewable energy sources is key to reducing emissions. The EHPA say that industrial heat pumps could deliver around 10% of the total final energy consumption of Europe’s industrial sector (about 2000 TWh) with 37% of the industrial process heat required currently below 200°C.
As an added incentive, the EHPA reveals that nearly all European countries provide financial subsidies or support for companies investing in industrial-sized heat pumps, available in the form of grants, loans, or tax rebates.
Heat pumps in the dairy sector
In the context of dairy manufacturing, implementing heat pumps can facilitate the recovery of waste heat from various processes, such as waste water, cooling loads within the production processes and exhaust air.
Leon Schachtner is Product Manager Food & Beverage for E.ON Energy Infrastructure Solutions (EIS), based in Essen. As a product manager, he is focused on developing and delivering heat pump solutions for the food and beverage industry, drawing on his expertise in this sector. Schachtner explained how dairies are a perfect fit for heat pump technology.
“Dairies use a lot of energy and tend to be big sites, operating 24/7 due to the raw products like fresh milk carried in continuously” he says. “However, the savings come from the lower operating costs of using heat pump systems, and in particular, lower fuel costs over the lifetime, especially when replacing steam with hot water where steam is not really needed and kept due to grown infrastructure from ancient times. In addition, customers can use low or even negative electricity prices to their advantage: heat pumps load thermal storages when electricity is cheap and avoid price peaks when electricity is expensive, in contrast to gas, which has rather stable prices.”
Schachtner also notes that as well as a full transition to heat pumps, a more gradual, stepwise approach needs to be taken, where the transition is phased over time to align with the customer’s decarbonisation targets on their path to net zero. Schachtner adds that consumers can take advantage of innovations throughout the system’s lifetime by updating heat pump systems as the underlying technology advances.
Challenges of transition
Transition is not without challenge, says Schachtner, including operational concerns about the reliability of heat pump technology, as it is rather new in the industrial setting compared to traditional gas boilers and chillers. Customers also worry about integrating the technology into existing operations in a way that minimises disruption.
“When transitioning to the heat pump solution, it needs to fit in during ongoing operations,” explains Schachtner. “You simply can’t close the factory for three months. So, we need to find clever solutions and we do this by very careful planning. We can also, for example, use containerised systems, using a modular heat pump system, which you can pre-assemble, test, and then deliver and connect, instead of building everything on site.”
When it comes to initial cost and funding, Schachtner says, E.ON can help with this too. Regulatory changes and available funding schemes can play an important role in supporting the adoption of heat pump technology, as they help address the higher initial investment costs.
“Initial costs are higher because the system is more complex compared to the traditional setup,” notes Schachtner. “Funding is an integral part, hence we help our clients. They don’t need to navigate this on their own – we support them.”
Another challenge is ensuring sufficient capacity at the grid connection point, as the local infrastructure likely needs to be expanded significantly to accommodate the increased electrical load.
Case studies
There is little doubt that heat pumps will be integral to the sustainable dairy operations of the future, driving efficiency and reducing environmental impact.
E.ON’s implemented heat pump projects within the sector include several projects for dairy processing firms, by its subsidiary AirSon, an engineering consultancy focused on F&B, Pharma and Hi-Tech.
This includes a turnkey solution for an international dairy company. E.ON’s customer has ambitious decarbonisation targets with becoming net zero by 2050. E.ON has supported the customer in its decarbonisation journey and transition to a fossil-free future with a turnkey EPC-contract to replace an electrical steam boiler and heat pump with a state-of-the-art heat pump, a new electrical boiler and a new transformer.
Another customer, located in Northern Europe, focuses on sustainability and reducing its carbon footprint. E.ON was able to support by focusing on energy efficiency and best practices across their production sites, including a heat pump solution that produces both heating and cooling for production processes, load optimisation and an ice water chiller installation, leading to significant cost savings and CO2 reductions.
Also, E.ON is currently designing a heat pump system for a dairy in Germany focusing on providing temperatures up to 100°C, proving real interest and potential in the market.
As solutions provider, E.ON independently designs the solutions and works with all OEMs. But to fully utilise the technology and innovations, E.ON has a collaboration agreement with heat pump maker Heaten[iv], whose piston-based technology stands out due to its power range, efficiency and flexibility – the heat pumps range from 1 to 8 MWth and can be combined to provide over 50 MWth. Heaten heat pumps deliver hot water or steam up to 200°C by utilising waste heat. E.ON sees this collaboration as a ‘good fit.’ “We aim to do joint pilot projects together and hope to benefit from our collaboration by advancing the technology in concrete projects,” says Schachtner.
Looking forward
According to Schachtner, “heat pumps are not just applicable to the dairy industry”. The principles and challenges discussed here are also relevant across various types of industrial food and drink production facilities. He says that the next challenge is addressing higher temperature levels beyond 100°C (beyond pilot applications) while still increasing efficiency and keeping system cost under control.
“While this is not cost-efficiently and reliably possible as of now, I expect this to change soon, and then there will be even more applications,” Schachtner says. “Heat pump technology will be the standard for decarbonisation in ten years’ time. Optimisation and more integrated solutions, not just hardware, is what we already offer – but we will drive even more. We already have some first solutions in place, but definitely want to go bigger. We see huge potential, despite all the challenges in electrification in the next decade due to grid constraints and the competitive demand by mobility, home heating and other industrial sectors, to have affordable electricity on grid capacity and volume.”
For more information on E.ON’s innovative solutions for the food and beverage industry, download the free white paper below.
[i] https://www.eea.europa.eu/publications/decarbonisation-heating-and-cooling
[ii] https://climate.ec.europa.eu/eu-action/climate-strategies-targets/2050-long-term-strategy_en
[iii] https://www.ehpa.org/news-and-resources/publications/heat-pumps-in-europe-key-facts-and-figures/
[iv] https://www.heaten.com/